Over the last 8 years, Mastermoulders has been investing heavily in 3D printing technology to help meet the demands of our customers. With our fully equipped 3D printing studio we are able to, quickly, turn your idea into reality.
3D printing is usually the second step, after the initial design stage, when bringing a new product to market. Having everything in house means that we can iterate a design very quickly and bring your product into production within a matter of weeks.
We have a wide range of materials and processes to choose from.
We can handle anything from a one-off prototype to batch production of 3D printed parts.
Technologies Available
FDM – Fused Deposition Modelling
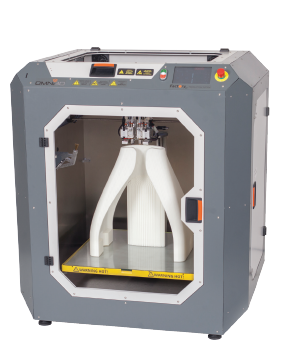
Fused deposition modelling or FDM is the selective deposition of melted material, layer by layer. The materials used are thermoplastics and come in the form of filament.
FDM is the most common form of 3D print and is the cost effective.
We are able to print ABS, Nylon, HIPS, PETG and many other engineering plastics up to 500 x 500 x 500mm.
We can finish all 3D prints to a very high standard with our highly skilled in-house painting and finishing team.
SLA – Stereolithography
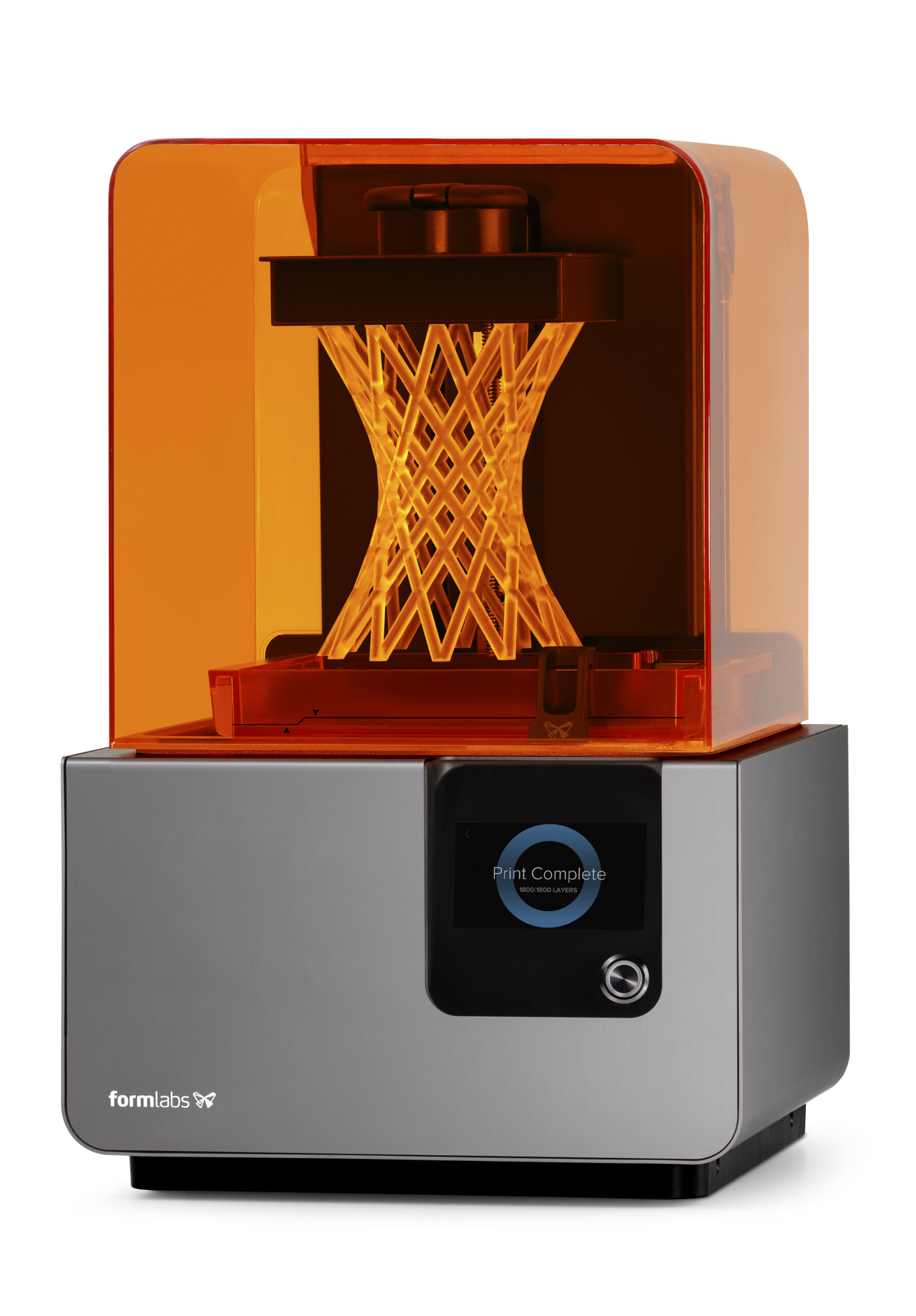
SLA or stereolithography is commonly known as resin 3D printing. These machines use a light source (laser) to cure liquid resin into hardened plastic, layer by layer. The resulting object is then washed and post cured using a UV oven.
This type of 3D printing has the highest resolution, accuracy and surface finish of all the 3Dprinting processes.
We have a large library of materials at your disposal with a wide range of optical, mechanical, and thermal properties to match those of standard, engineering, and industrial thermoplastics.
SLS – Selective Laser Sintering
SLS or Selective Laser Sintering is process in which a laser selectively sinters a plastic powder, fusing the particles together and building a part layer by layer.#
SLS is used to create strong, functional prototypes and small production runs. It also offers a high degree of design freedom due to the way the part is supports within a powder bed.
We do not have the technology in house but we have been working with our subcontractor for SLS printing for many years, and parts can normal be turned around in a couple of days.